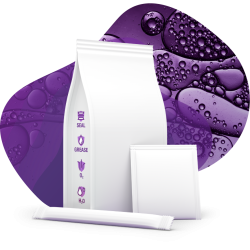
Focus on barrier papers
The future of flexible packaging is paper-based.

Consumers and food manufacturers alike are increasingly looking for alternatives to plastic packaging. René Köhler, Director Paper & Packaging Solutions at Sappi Europe, explains in an interview how Sappi, as a specialist for packaging and specialty papers, is meeting the growing requirements thanks to over 10 years of experience in the production of barrier papers. The focus is on product protection, adaptation to existing packaging lines and recyclability.
Consumers and thus food manufacturers want alternatives to plastic packaging. In this context, interest in barrier papers has increased sharply in recent years. What are the main challenges in terms of functionality? And how do you overcome them?
Three points in particular are important for our customers. First, product protection. It is crucial that the protection of the product is not compromised compared to the current packaging. An example of this is ensuring a certain best-before date. A reliable and secure supply chain is also important for retailers.
Secondly, the barrier papers should ideally run on existing packaging lines. Our customers want to avoid, at all costs, major investments in machine components or even in entire systems in order to switch to a new material. In such cases, optimisations are necessary. For this reason, we work closely with packaging machine manufacturers to carry out preliminary tests. Often it depends on the settings of the machines, which make it possible to switch from conventional materials to new, more sustainable materials.
The third and most important point is to use a material that can actually be recycled in the paper waste stream, rather than ending up as ordinary waste. This is not the case with much of today's packaging and is the main driver for our customers. If we can meet the first two points and also guarantee this third aspect, this is crucial for the choice of barrier papers.
For which dry products are barrier papers suitable and not suitable? Where might normal paper or glassine be sufficient?
There is no general answer to this question as the term "dry products" covers a very wide range. These include products such as cereals, coffee, dried fruit, flour or ready-made soups. Each of these products has specific demand and therefore requires an individual barrier to ensure effective protection – especially in the case of food to ensure the best-before date.
Standard base paper does not offer any barrier and is therefore only as a laminate suitable to protect the goods. Glassine, a high-density paper, is largely grease-proof, but offers no protection against moisture. For example, it is suitable for packaging butter, but is less suitable for other applications. In addition, neither standard paper nor glassine do provide a sealability. Barrier papers, on the other hand, offer a combination of optimally adapted protection and functionality that make them ideal for many dry products.
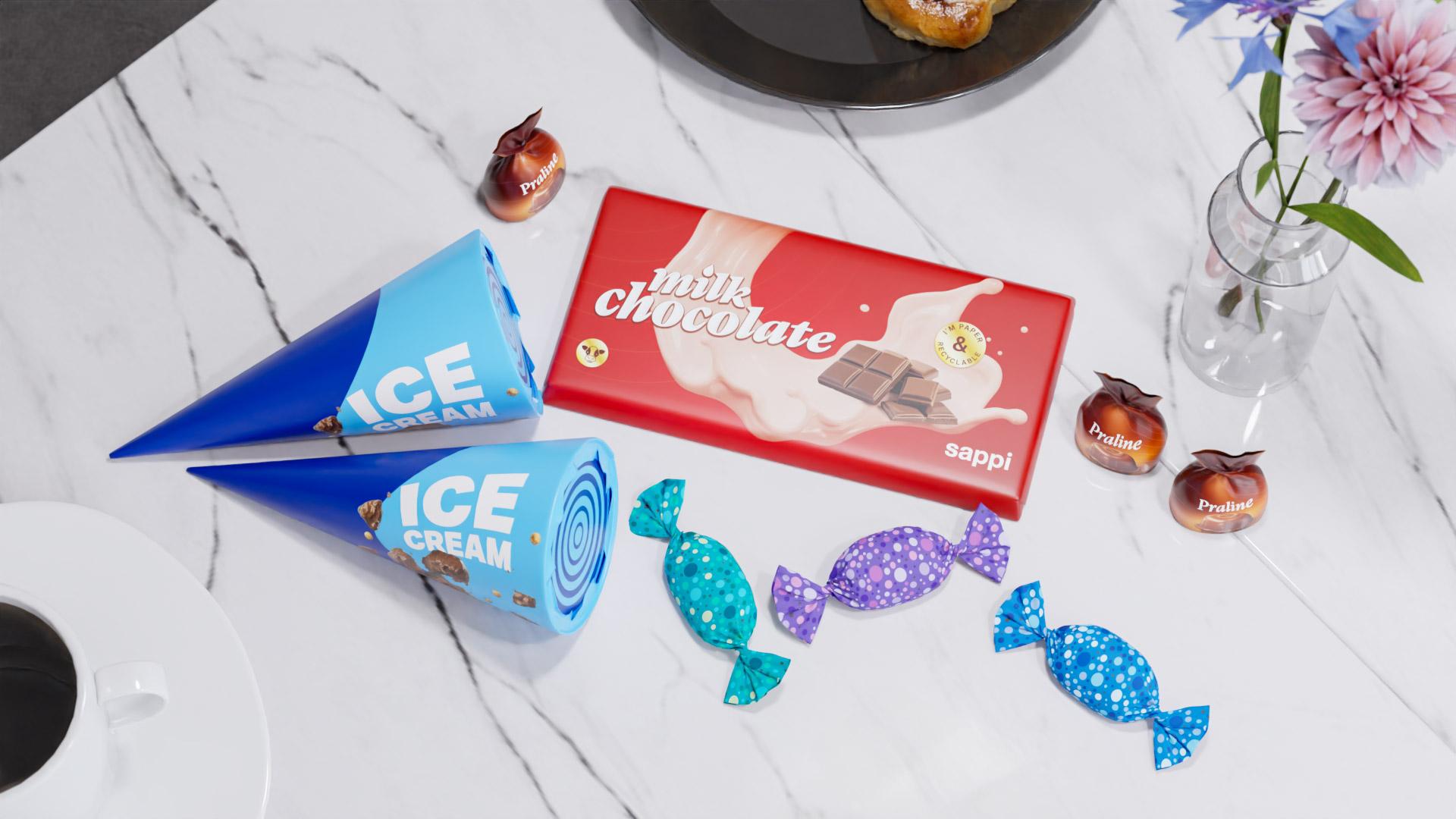
How do you test the functionality of the barrier papers?
We use special measuring instruments to thoroughly test our barrier papers. We test the permeation, i.e. the permeability of oxygen, water vapour, grease resistance, or mineral oil (MOSH/MOAH) in order to ensure the necessary protection in each case. For papers that need to be heat-sealable at the same time, we also check the achievable seal-strength. All these measured values are then shown in the respective data sheets.
How flexible are barrier papers in terms of their runnability on existing packaging lines or their different thicknesses?
Our barrier papers can be processed on existing packaging lines – but all this depends on the type of packaging you want. A small, individually packaged bar has different requirements than a large bag containing many small products. The processability of the packaging material into the finished packaging also depends on the respective packaging machine, which is why we sometimes rely on the support of the machine manufacturer.
In most cases, the technicians of the brand manufacturers manage to adapt the existing packaging lines to run paper-based packaging materials – especially barrier papers – on their own. An adjustment is often necessary because the plastic films and laminates used today are very thin, flexible, robust and tear-resistant. Paper, on the other hand, is less tear-resistant and requires more sensitivity in the packaging process. There are cases where the machines can be converted 1:1 to paper-based packaging, but this is the exception.
Which legal requirements play a role in this area (e.g. special safety in the case of direct food contact, EU regulations to increase recyclable packaging)?
The legal requirements are a central guideline for us in the development of paper-based solutions, and we strictly adhere to them. In the field of food packaging, for example, our barrier papers must always be suitable for direct food contact. In addition, all materials entering our production facilities must be approved for direct food contact. We have to prove this suitability and declare compliance accordingly. Since we cannot always provide this evidence ourselves, we work with external test laboratories that check food safety and issue us with the necessary certificates. Our customers demand these documents from us.
When new legal requirements, such as those to increase the recyclability of packaging, come into force, we naturally comply with them. Basically, our goal at Sappi is to ensure that packaging made from our papers is recyclable at the end of its life cycle. At the same time, the specific needs of our customers are always decisive for us.
How do you check the recyclability?
At Sappi, we have established, internal control mechanisms. Our papers are first tested in an internal, non-accredited laboratory according to specified measurement methods, according to CEPI or the PPWR (Packaging and Packaging Waste Regulation). This allows us to determine at an early stage whether the papers meet the specifications and to make adjustments if necessary. The papers are then sent to accredited, external test laboratories for testing, who issue us with the corresponding certificates. Our customers receive these certificates as reliable proof of the recyclability of the material.
How do you deal with the issue of sustainability in raw materials (production in South Africa, timber transports to Europe, FSC or PEFC-certified forests)?
Sappi has implemented transparent practices by using internationally recognised, independently verified certification systems including the Forest Stewardship Council™ (FSC™ N003159); Programme for the Endorsement of Forest Certification (PEFC/01-44-43) and the Sustainable Forestry Initiative® (SFI®). Knowing the origin of woodfibre is essential for responsible sourcing of wood and pulp. All of Sappi’s mills have been FSC Chain of Custody (CoC) certified since 2008, and all mills (except Stanger Mill and Lomati Sawmill) are also PEFC CoC certified, including SFI in the USA. Our 400,000 hectares of owned and leased plantations in South Africa are both FSC and PEFC certified. We use the raw materials from these forests exclusively for local production. This means that no wood or other raw materials go from South Africa to Europe. Depending on our mills, we do have a pulp integration. We source the wood required for the production of pulp from a radius of approximately 150km of the respective site.
In principle, we can offer our products on customer request as FSC™ certified or PEFC certified depending on credit availability.
When a customer orders certified material, the delivery and sales documents will always carry the respective claim and our certification number(s). And thus each delivery is verified to originate from controlled, non-controversial sources per FSC and PEFC standards.
What about price? Are barrier papers more expensive?
There is no general answer to this question. It depends heavily on the comparative material. The range of materials used today ranges from mono-plastic films to multi-layer laminates that are not comparable in price. At first glance, barrier papers may seem more expensive. However, it must be taken into account that in some countries there are incentives, i.e. premiums for materials that are easier to recycle. This should definitely be included in the total cost of ownership. In addition, anyone who places packaging on the market must pay a recycling levy, which depends heavily on the raw material used. For brand manufacturers, it is therefore of great importance whether a barrier paper or plastic film or laminate is used. Paper-based mono material like barrier paper solutions offer an advantage in this context.
What is Sappi's USP?
As a pioneer in this field, Sappi started producing barrier papers more than 10 years ago. Therefore, we have built up appropriate experience and competence that not everyone in the market can boast – and we are currently the manufacturer with the largest range of barrier papers.
Thanks to pioneering dispersion technology, we produce these in such a way that they can be easily recycled in the paper waste stream. Our offer is rounded off by competent advice that supports customers in finding the right product. On this solid foundation, we are continuously expanding our already broad portfolio with new products.
Instead of offering oversized standard products, we develop tailor-made solutions that are precisely tailored to the barrier requirements of our customers. This allows us to react quickly and flexibly to individual needs.