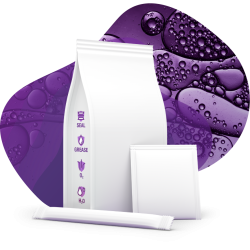
Barrier papers or plastics? It’s not so simple
- This article was published by Packaging Europe on February 16, 2021
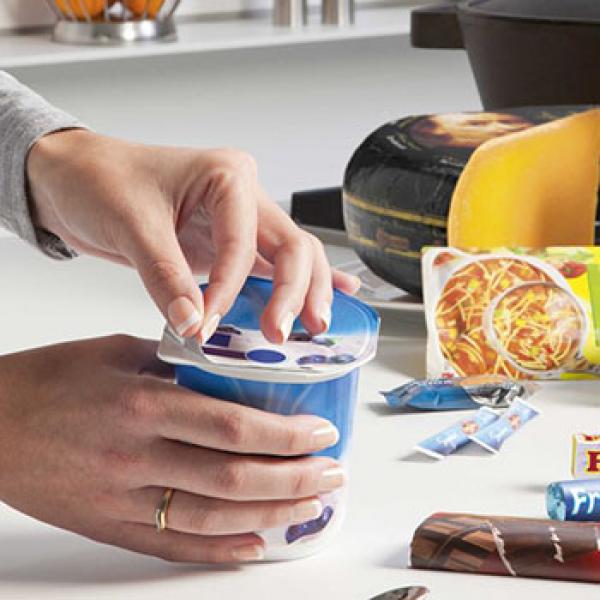
Victoria Hattersley spoke with René Köhler, Head of Business Development Packaging Solutions at Sappi Europe, to delve into the topic of barrier papers and Sappi’s aim to ensure their wider use as the industry begins to phase out fossil-based materials.
When it comes to barrier packaging, the market is looking very different than it did 10 years ago. For years, non-recyclable polyethylene coated, multilayer laminated flexible materials and aluminium have been the main options for packaging perishables. However, the situation has changed. Although they are certainly not in a position to ‘replace’ plastics, we see the introduction of increasingly sophisticated barrier papers each year.
But not all barrier papers are equal. To put it bluntly, some are high barrier while some are not so much. How do we sort out the genuinely game-changing solutions from the greenwash?
“On the market a lot of people claim they have barrier papers, but what does this really mean? Any paper that contains a layer of another material can be called a ‘barrier paper’ but that doesn’t mean it fulfils the demands of the market.”
He states that the ultimate aim for Sappi, as a barrier paper specialist, is to substitute aluminium and plastic multilayer laminates and bring in a truly sustainable alternative that meets all market demands in terms of performance. The company has already made strides in this direction, for example with its Sappi Guard Gloss 4-OHG – a one-side coated glossy paper with functional high barrier coating and heat sealability that is suitable for both food and non-food applications.
A common perception within the industry and beyond is that barrier papers can’t be recycled, as they must still contain some kind of polymer-based coating to protect the product. But René stresses that this is not that case – that it is possible to have a paper containing a polymer-based layer that could still be put into existing recycling streams; part of the problem, as we will see later, is that the recycling infrastructure itself is not set up for this. Sometimes, with such complex topics, it can be useful to come back to a more fundamental question, and so we ask:
What exactly is a plastic?
The answer, most of us would say, is pretty simple: plastic is the umbrella term for the wide range of synthetic or semi-synthetic materials on the market today made from an ever-growing range of organic raw materials such as fossil fuels, cellulose, gas, salt and so on.
René, however, argues that we need to clarify – or even redefine – the nature of plastics if we are to challenge commonly held beliefs about barrier papers. “If you have a rigid plastic package, then that is a structural plastic and clearly that can’t be placed in the paper recycling stream. But what we are adding to our papers are very thin functional layers of polymers. We believe that you need to distinguish between the two – structural and functional – because with the latter, provided they are engineered in the right way, it should be possible to use the paper waste stream as the functional layers can be removed from the fibres. We don’t state our barrier papers are polymer-free because that would be false; it’s all about how you define it.”
Are we over-engineering?
It’s an interesting point, but Sappi is aware that it will take more to convince even more brand owners to make the switch to paper for their FMCG products. It may, indeed – dare we say it – come down to a compromise; a re-evaluation of exactly how long they really need their products to last on the shelf. Are we asking too much of packaging at the expense of the environment? René seems to suggest that in some cases, some complex barriers we use today – while impressive – may be over-engineered.
“Brand owners often come to us with very high functional requirements, but right now the challenge for them is to identify which protection is really needed for their products. Are we willing to continue in the same way or can we make a compromise on shelf life in order to utilise more sustainable materials? I think in many cases it is possible, if we can just change mindsets a little.”
None of this is to say that we should sacrifice functionality – clearly, increased levels of food waste would be the worst scenario so barriers still need to provide the correct moisture, oxygen, heat, aroma barriers and so on. It’s simply that FMCG goods may be over-packaged when we consider their actual shelf-life requirements. Time for a re-think, perhaps? Even using barriers that protect for nine months rather than 12 could make a significant environmental difference.
“We try to tailor-make these applications according to the need. So, we discuss individual projects with brand owners, work out their minimum criteria and which packaging material from our end will be suitable for their application.”
What must the wider industry do?
Of course, it’s not just the brand owners; more importantly, the industry itself needs to adapt to the inevitable surge in barrier papers we will see in the coming years. The issue is that, up to now, the majority of papers being recycled have been graphical papers, and that is what the recyclers are used to. This can’t be the case going forward, says René: the recycling infrastructure must be prepared to process barrier materials on the necessary scales.
“Is the infrastructure completely ready now? Frankly, no, so there’s a lot to do. Some recyclers are very keen to include barrier papers and others are more used to the ‘pure’ papers. We have to get the message across that our barrier papers are very recyclable and it’s not complicated to include them in the recycling stream, as long as the industry is prepared to make the small changes required.”
There’s also the production side to consider: manufacturers may have concerns regarding the ability of paper to run on existing converting and packaging machines. Would it require huge investment – possibly even an entire equipment overhaul – if they are to handle the volumes of barrier papers Sappi and others hope we will see in the future?
René argues that it does not, although he can understand the concerns: “These packaging lines are used to working with films, but of course paper is completely different: easy to tear, not as puncture-resistant and so on. However, contrary to belief, this does not require huge outlay. It is our aim that these barriers should be able to run on existing packaging lines, with just a few modifications, so brand owners would not have to invest in new technologies.”
We need plastic – but how much?
There’s a question we come back to time and again when talking to paper producers, and it’s a big one: What would Sappi say to those who argue that the overall environmental impact of manufacturing paper is higher than for plastics? We’ve heard compelling rebuttals to this – that the paper industry is also a high user of renewable energies, for example, or that we need to factor in the entire LCA – but it remains the case that paper does require a high amount of energy and resources to produce when compared to plastic.
For Sappi, it comes down to a kind of pragmatism: we have to work with the realities of today. “When it comes to energy consumption, yes paper is intensive but we should not lose sight of the problem posed by plastic waste. It is not so much Europe that is the issue, where the infrastructure is improving, but more the developing world – Asia and the Middle East, for example – where the recycling infrastructure is not in place at all.”
In these cases, he says, there is a mountain to climb: not just in setting up the recycling systems but in bringing about a behavioural change in consumers so that plastics are not simply being put back into the environment, where they will last for hundreds of years – unlike paper, which will disappear. Both these changes – infrastructural and behavioural – while certainly possible could well take decades, and René argues that we do not have that amount of time to wait.
Chemical recycling is of course a very exciting field of development which could change the landscape when it comes to building a circular economy for plastics – but again, this is in the very early stages and it will be years before we can expect it to become an industry reality. Paper, on the other hand, is already the most widely recycled material in the world, putting it in a very strong position to meet the ambitious new recycling targets set by the EU, as René explains. “If we take the global figures for paper and board materials, we are at 70-80% recycling rates and the target is up to 90% so it’s completely different to plastic where the global recycling rate is something like 14%.”
But Sappi is not looking to demonise plastic. “Of course, we need this material – there are cases where it is the only real solution – but there are certain areas where paper can and should play a much bigger role. The clear direction for the packaging industry as a whole is to strive towards 99% recycling in both streams: mono-plastics and barrier papers. Multilayers will naturally fall by the wayside in our view because they can’t be recycled” (although some companies are working on the latter).
The alternative use of biopolymers is not realistic either on a wider scale – at least not for the immediate future. “There was also a question mark as to whether we should go with compostables for emerging markets, but it is more expensive and the performance of these materials is not yet totally proven. I also worry that by offering compostables we are encouraging people to throw it into nature rather than consider the possibilities for recycling.”
Much more is possible
I should add here that when stating we need to work within the market constraints we face today, it does not mean we can’t look to a future where more is possible. Just using the example of paper: the kinds of barrier solutions people might have said were unfeasible in the past, we now see on supermarket shelves. Sappi’s aim is to continue reducing the amount of plastic it uses, until finally (a long time in the future, admittedly) there will be no need for a polymer barrier at all. “First of all, we wanted to show the world that it is possible to create a high barrier paper,” says René. “With the next generations of these papers the barrier layer will be even thinner without sacrificing performance. We will also be working to improve puncture-resistance compared to plastic.”
He feels that the biggest problem is not creating the barrier performance – this will come, as technology evolves – but rather the lack of support to push the paper agenda. The ideal situation, he tells me, would be a unified recycling system in place for the EU, with clear instructions on where consumers can place paper packaging. Finally, the thresholds across Europe need to be changed and harmonised: there should be new thresholds to allow a higher polymer content in barrier papers, otherwise the substitution of plastic and foil-based materials would be impossible to reach in areas such as Germany, where the maximum allowable content is 5%. There’s no doubt that the industry still has much to do when it comes to wider industry acceptance of barrier papers, but Sappi is confident they will come to hold a bigger share of the market. In short, change is coming: it’s just not going to happen overnight.
Packaging Europe (February 16, 2021):
https://packagingeurope.com/sappi-barrier-papers-or-plastics-not-so-simple/